Introduction
Valves play a crucial role in industrial operations, regulating fluid flow in various systems. However, valve failures can lead to costly downtime, process inefficiencies, and safety risks. Understanding the most common valve failures and how to prevent them ensures optimal performance and longevity.
1. Leakage (Internal & External)
Causes:
-
Worn-out seals or seats
-
Corrosion or erosion
-
Improper installation
-
Excessive pressure fluctuations
Effects:
-
Fluid loss and contamination
-
Pressure instability
-
Increased maintenance costs
Prevention:
-
Regular inspection and seal replacement
-
Proper material selection for corrosive environments
-
Ensuring correct valve installation
2. Valve Sticking or Hard to Operate
Causes:
-
Buildup of debris or scale
-
Lack of lubrication
-
Misalignment of components
Effects:
-
Difficulty in operation
-
Higher energy consumption
-
Potential safety hazards
Prevention:
-
Regular cleaning and lubrication
-
Use of self-cleaning valves where applicable
-
Proper alignment during installation
3. Cavitation Damage
Causes:
-
High-pressure drops causing vapor bubbles
-
Sudden flow rate changes
-
Poor valve sizing
Effects:
-
Pitting and erosion of internal surfaces
-
Excessive noise and vibration
-
Reduced valve lifespan
Prevention:
-
Using anti-cavitation trims
-
Selecting the right valve size and type
-
Maintaining steady flow conditions
4. Corrosion & Erosion
Causes:
-
Exposure to harsh chemicals
-
High fluid velocity
-
Incompatible valve material
Effects:
-
Structural weakening
-
Increased likelihood of leaks
-
Frequent replacements required
Prevention:
-
Selecting corrosion-resistant materials
-
Using coatings or linings
-
Ensuring proper flow rate management
5. Seal or Packing Failure
Causes:
-
Excessive wear or aging
-
Extreme temperature fluctuations
-
Incorrect packing installation
Effects:
-
Leakage and contamination
-
Process inefficiencies
-
Increased maintenance downtime
Prevention:
-
Regular seal replacement
-
Using high-quality packing materials
-
Maintaining stable operating conditions
6. Actuator or Positioner Failure
Causes:
-
Pneumatic or electrical faults
-
Mechanical wear
-
Software or calibration issues
Effects:
-
Inaccurate valve positioning
-
Process control inefficiencies
-
Potential safety concerns
Prevention:
-
Routine calibration and diagnostics
-
Using high-quality actuators and positioners
-
Immediate troubleshooting of control system alerts
7. Water Hammer Damage
Causes:
-
Sudden valve closure
-
Rapid fluid velocity changes
-
High-pressure surges
Effects:
-
Pipe damage and leaks
-
Valve seat and disc damage
-
System fatigue and failure
Prevention:
-
Installing slow-closing valves
-
Using surge protection devices
-
Implementing gradual pressure control
8. Incorrect Valve Selection or Sizing
Causes:
-
Mismatched valve type for the application
-
Undersized or oversized valves
-
Lack of flow condition analysis
Effects:
-
Inefficient flow control
-
Frequent breakdowns
-
Increased operational costs
Prevention:
-
Conducting a thorough needs assessment
-
Consulting with valve specialists
-
Using software tools for proper sizing
Conclusion
Preventing valve failures starts with understanding their causes and implementing proactive maintenance strategies. KV Controls provides high-quality valve solutions tailored to various industrial applications, ensuring reliability, efficiency, and safety. Contact us today to find the right valves for your system and avoid costly failures.
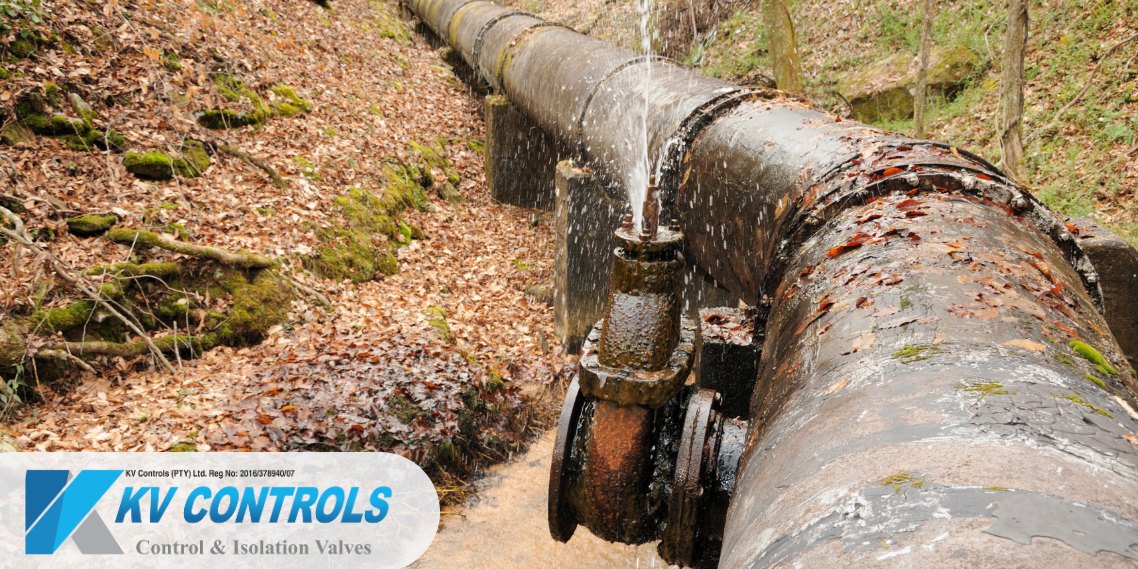