How to Maintain and Extend the Life of Industrial Valves
Industrial valves play a crucial role in controlling the flow of liquids, gases, and steam in various industries. Regular maintenance is essential to prevent failures, enhance performance, and maximize operational efficiency. Below, we dive deeper into key maintenance strategies to extend the life of your industrial valves.
1. Regular Inspection & Monitoring
Routine inspections are the first line of defense against valve failure. Identifying early signs of wear, leaks, or pressure irregularities allows for timely interventions. Key inspection steps include:
- Visual Checks: Examine valves for cracks, corrosion, and leakage.
- Leak Detection: Use ultrasonic devices or infrared cameras to identify small leaks before they escalate.
- Torque Testing: Ensure valves are operating within proper torque limits to prevent undue stress.
- Vibration Monitoring: Abnormal vibrations can indicate mechanical wear or improper installation.
By implementing predictive maintenance tools like condition monitoring sensors, industries can minimize unexpected breakdowns and optimize valve performance.
2. Proper Cleaning & Lubrication
Dirt, debris, and rust accumulation can cause industrial valves to seize, affecting efficiency and reliability. Cleaning and lubrication must be done using manufacturer-recommended materials.
- Cleaning Methods:
- For metal valves, use chemical solutions that remove rust and buildup without causing material degradation.
- For plastic or lined valves, avoid harsh solvents that could weaken structural integrity.
- Lubrication Guidelines:
- Use high-quality, temperature-resistant lubricants suited for your application.
- Ensure lubricant compatibility with the valve’s seals and packing.
- Apply lubrication at recommended intervals to prevent excessive friction and wear.
A well-maintained lubrication schedule reduces operational resistance, minimizes wear, and enhances sealing efficiency.
3. Correct Installation & Alignment
Improper valve installation is a major cause of premature failure. Ensuring correct alignment and mounting prevents undue stress on valve components.
- Key Installation Considerations:
- Align the valve properly with piping to avoid stress points.
- Follow torque specifications for bolts and flanges to prevent leakage or warping.
- Ensure correct actuator positioning for smooth operation.
Poor alignment can lead to valve body strain, increasing maintenance costs and reducing lifespan. Proper installation ensures reliability and optimal functionality.
4. Pressure & Flow Control
Excessive pressure and erratic flow rates can significantly shorten the life of industrial valves. Proper regulation prevents damage caused by high-pressure surges and cavitation.
- Best Practices for Pressure Management:
- Install pressure relief valves to manage sudden surges.
- Maintain system pressure within manufacturer specifications.
- Use flow control devices to prevent rapid fluctuations that cause water hammer effects.
Keeping operating conditions stable ensures valves function efficiently without excessive wear.
5. Material Selection & Corrosion Prevention
Choosing the right valve material for the application is crucial in preventing premature corrosion, erosion, and material degradation.
- Common Valve Materials & Their Applications:
- Stainless Steel: Ideal for corrosive environments and chemical processing.
- Brass: Suitable for water and gas applications.
- PVC & PTFE-Lined Valves: Best for highly corrosive fluids.
- Carbon Steel: Used in high-pressure industrial applications.
To further prevent corrosion:
- Apply protective coatings, such as epoxy or Teflon, for added resistance.
- Store spare valves in a dry, controlled environment to avoid moisture damage.
6. Scheduled Servicing & Repairs
Routine servicing ensures that minor issues don’t escalate into costly failures. A preventive maintenance schedule should include:
- Seal & Gasket Replacement: Deteriorating seals can cause leaks and inefficiencies.
- Valve Actuator Calibration: Ensuring actuators respond accurately to control signals.
- Leak Testing & Pressure Testing: Verifying the integrity of valve seating and connections.
- Spare Parts Management: Keeping critical spare parts on hand for quick repairs.
Proactive servicing minimizes downtime and extends valve longevity.
7. Smart Valve Technology & Automation
The integration of intelligent valve positioners and automated control systems enhances efficiency, reduces manual intervention, and improves predictive maintenance capabilities.
- Benefits of Smart Valve Systems:
- Remote Monitoring: Detect issues before they cause failures.
- Self-Diagnostics: Automated alerts for maintenance needs.
- Optimized Performance: Continuous adjustments for efficiency and lifespan extension.
Upgrading to IoT-enabled valve monitoring systems allows industries to track valve health in real time, reducing maintenance costs and improving reliability.
Why Choose KV Controls?
At KV Controls, we specialize in high-quality industrial valves and expert maintenance solutions to help industries optimize performance and extend valve life. Our products are designed for precision, durability, and efficiency, ensuring seamless operation in demanding applications.
🔹 Expert Consultation – Get the right valve for your needs.
🔹 Maintenance Support – Optimize performance with expert servicing.
🔹 Advanced Technology – Smart solutions for long-term reliability.
Contact us today for premium industrial valve solutions and professional maintenance services.
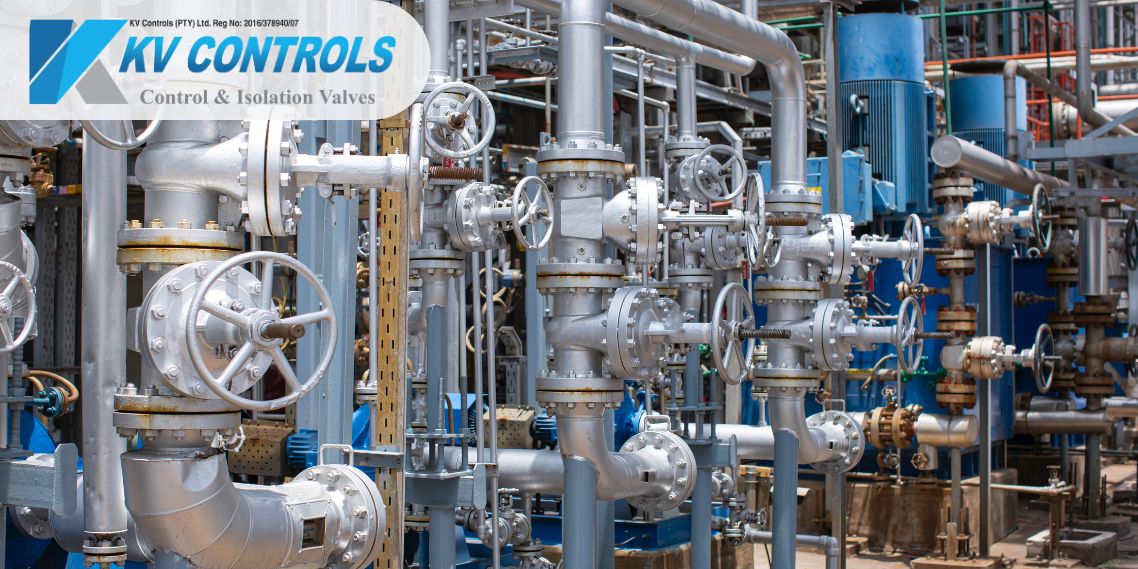