Understanding Actuators in Industrial Applications
Actuators play a critical role in industrial automation by controlling valves and other mechanical systems. These devices convert energy into mechanical motion, enabling precise control over various industrial processes. Choosing the right actuator—electric, pneumatic, or hydraulic—can significantly impact performance, efficiency, and maintenance costs. In this guide, we break down the key differences, advantages, and best use cases for each type to help you make an informed decision.
Electric Actuators: Precision and Control
How They Work: Electric actuators use an electric motor to generate motion, converting electrical energy into mechanical movement. They can be linear or rotary and are often integrated with digital control systems for enhanced automation.
Advantages:
✔ High precision and control, making them ideal for applications requiring exact positioning
✔ Energy-efficient for long-term use, consuming power only when in operation
✔ Low maintenance with fewer moving parts, reducing the risk of mechanical failure
✔ Easy integration with automation systems, making them compatible with IIoT and smart industry technologies
✔ Quiet operation compared to pneumatic and hydraulic alternatives
Disadvantages:
✘ Higher upfront costs compared to pneumatic actuators
✘ Not suitable for hazardous or explosive environments unless properly enclosed
✘ Limited force output compared to hydraulic actuators
Best For:
- Applications requiring precise positioning, such as robotics and manufacturing
- Industries using smart automation and IIoT systems for real-time monitoring
- Environments where clean, quiet operation is needed, such as laboratories and medical facilities
Pneumatic Actuators: Fast and Cost-Effective
How They Work: Pneumatic actuators operate using compressed air to generate motion. The pressurized air moves a piston or diaphragm, creating linear or rotary movement.
Advantages:
✔ Quick response time for high-speed operations, ideal for fast-moving industrial applications
✔ Cost-effective and lightweight, reducing installation costs
✔ Safe for hazardous environments as they do not generate sparks or require electricity
✔ Simple design with fewer failure points, leading to long-term reliability
✔ Capable of continuous operation without overheating
Disadvantages:
✘ Requires a compressed air system, which can increase operational costs
✘ Less precise control compared to electric actuators
✘ Higher energy consumption over time due to air compression losses
Best For:
- High-speed applications requiring rapid movement, such as packaging and assembly lines
- Industries like food processing and pharmaceuticals, where contamination risks must be minimized
- Explosive or hazardous environments where electrical sparks pose a risk
Hydraulic Actuators: Power and Durability
How They Work: Hydraulic actuators use pressurized fluid to create force, making them ideal for high-power applications. The hydraulic fluid moves through a system of pumps, valves, and cylinders to generate motion.
Advantages:
✔ High force output for heavy-duty tasks, providing unmatched power
✔ Reliable under extreme conditions, including high-pressure and temperature variations
✔ Handles high loads without compromising performance, making them suitable for demanding industries
✔ Longer operational life when properly maintained
✔ Resistant to vibration and shock, ensuring durability in rugged environments
Disadvantages:
✘ Requires hydraulic fluid, which can pose environmental risks in case of leaks
✘ More complex maintenance due to additional components like pumps and hoses
✘ Heavier and bulkier compared to pneumatic and electric actuators
Best For:
- Heavy machinery and industrial automation in construction, mining, and marine industries
- Applications requiring high force, such as lifting, pressing, and clamping
- Environments with extreme temperature or pressure variations, where other actuators may fail
Choosing the Right Actuator for Your Needs
When selecting an actuator, consider these factors:
- Precision & Control: If your application requires exact positioning and automation, electric actuators are the best choice.
- Speed & Efficiency: Pneumatic actuators offer quick response times and are ideal for high-speed processes.
- Power & Durability: For applications needing high force and rugged reliability, hydraulic actuators are unmatched.
- Environmental Conditions: If your industry operates in hazardous areas, pneumatic actuators offer spark-free operation, while hydraulic actuators handle extreme conditions well.
- Maintenance & Cost: Electric actuators have lower maintenance costs in the long run, while pneumatic and hydraulic systems may require additional upkeep for air compressors or fluid systems.
Why Choose KV Controls for Actuation Solutions?
At KV Controls, we supply high-quality electric, pneumatic, and hydraulic actuators tailored to your industry’s needs. Our extensive product range ensures that we have the right solution for your specific application, whether you need precision control, high-speed operations, or heavy-duty power.
Our team of experts is ready to assist you in choosing the most efficient and cost-effective actuator for your industrial process. With years of experience in the field, KV Controls is a trusted partner for industries across South Africa, providing top-tier products and technical support.
Contact us today to explore our range of industrial actuators and find the best solution for your application. Let KV Controls help you enhance efficiency, improve automation, and optimize performance in your operations.
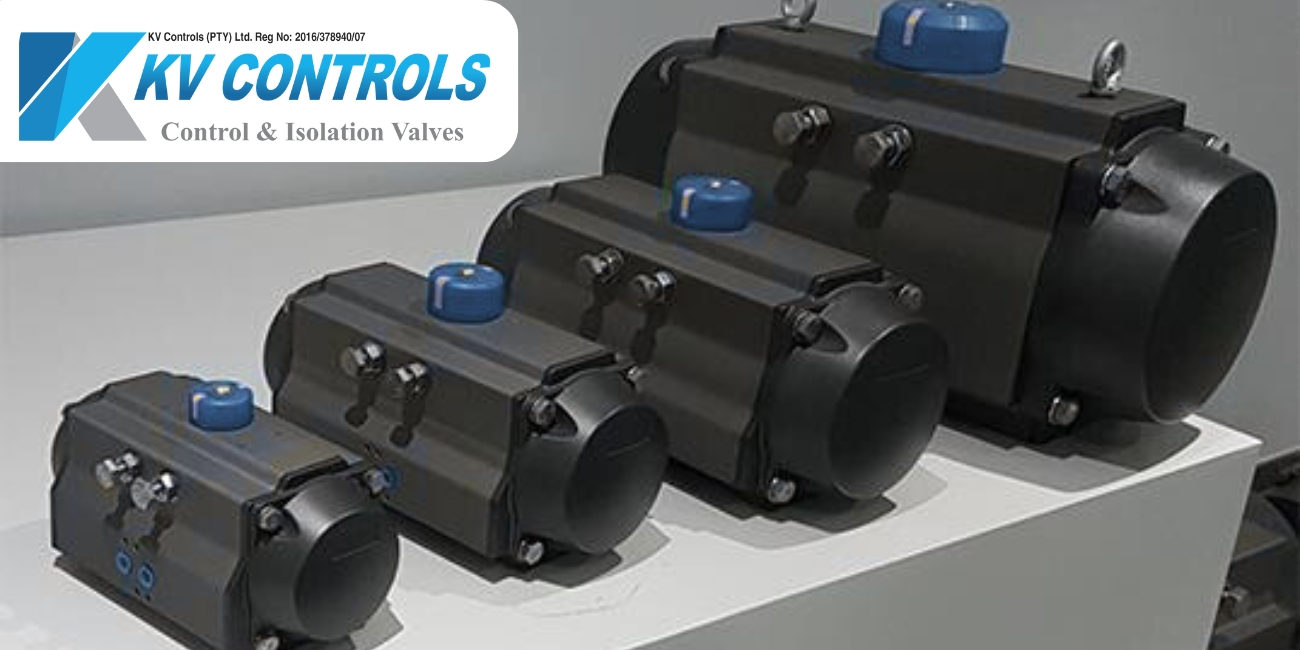